大众公司的高尔夫汽车生产线在两台库卡机器人的密切配合下,灵活而又悠闲地为车身安装车门,两台智能机器人配合非常默契,彼此了解并实时沟通,以期保证自己的每个动作都在最适当和最短的时问内完成。
这是在德国汉诺成举行的工业博览会上西门子公司展台发生的一幕,该模型旨在描绘未来制造智能化软件与高性能的生产硬件如何紧密协调工作的场景。
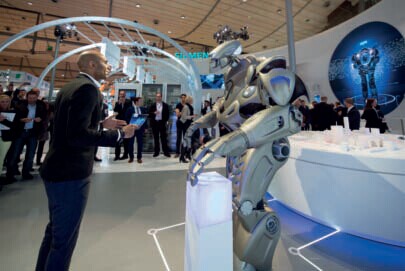
在4月7日开幕的汉诺成工业博览会吸引了全球65个国家和地区的约5000家厂商参展,当德国总理默克尔在荷兰展台欣然接受机器人小萝莉递来的郁金香时,制造业的智能化大潮持续在偌大的汉诺成博览会上延伸,对未来制造的探索之旅电正式在这里启程。
制造业占GDP 23%份额的德国提出了工业4.0的概念,默克尔认为未来工厂中的机器、设备、零件之问可以自由沟通,智能工厂能够自行运转。
西门子股份公司管理委员会成员、工业业务领域CE0鲁思沃把当前制造过程分成产品设计、生产规划、生产工程、生产实施和服务五个阶段,并把其称作为工业3.X,即当前可以提供全面数字化工厂的解决方案,但距离工业4.0还有很大差距。
在西门子展台,尼桑一款新型赛车在产品设计阶段采用了数字虚拟软件,模拟了车身的曲面设计,最大限度地减少了赛车高速飞驰时的空气阻力。经过优化设计的尼桑赛车百公里加速只需要2.5秒,而其他赛车一般需要9秒。这是一款把传统内燃机推进系统和电动系统结合起来的混合动力赛车,最高时速可达300公里,是当今世界上最快的电动赛车。
西门子3D可视化软件正在模拟法国道达尔钻井平台的生产环境,让每个参观者如临其境,在虚拟现实的模型中,可以直接获取即时的生产数据,预知生产环境,让参与其中的人更有安全感。
工业4.0的核心理念之一就是现实工厂与虚拟工厂的无限接近,从这个角度看,我们的一只脚似乎已经踏进了未来制造的大门。
产业集成
Tucher是德国北巴伐利亚州众多啤酒厂当中的一家,曾经是纽伦堡贵族的家族企业。本刊记者在参访体味当地啤酒文化的同时,还深刻感受到啤酒在生产过程中集成化、自动化设备和软件的高度应用。
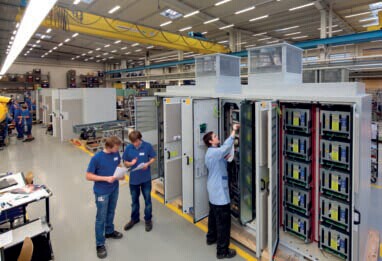
正是这些包括西门子在内的工业集成方案提供商保证了啤酒口味的多样化和每种口味的精确度,清爽、苦涩、酸味等十几种啤酒口味不单单是每天品尝工程师们舌尖上的幸福,更是工业智能和集成应用伟大作用的生动体现。
本次展会把“产业集成”设立为主题,智能工厂是产业集成的目标,而集成的装机,在西门子开放工程架构下,SICK公司的智能传感器、库卡公司的机器概念在中国今年春节联欢晚会上已有体现。201 4年春节联欢晚会可实现舞台布景中五个LED屏幕的自由移动,由于节目是现场直播,舞台技术以及设备的可用性必须得到保证。
西门子巧妙地把集成的思想应用其中,为该项目提供了全集成驱动系统,该系统由电机和运动系统组成,后者直接集成在变频器的闭环控制模块里,所有组件在传动系统里协同配合,从而确保了舞台设备的可用性和安全运行。
记者在工程展区看到一台生产线末端包装机,在西门子开放工程架构下,SICK公司的智能传感器、库卡公司的机器人以及其他自动化部件,在一个名叫“博途”的软件调配下自主进行着包装动作,这一场景也是驱动系统与自动化系统进行集成的体现。
西门子驱动技术集团CE0方润朗(Ralf_Michael Franke)先生在解释未来制造全集成驱动系统的变革方向时说,过去集成概念只在个别产品上进行优化,比如电机、齿轮、变频器和联轴器的一般性组合,而现在则是整个驱动链条上的功能集成、自动化层面的集成以及涵盖整个产品生命周期的集成。
全集成驱动系统专业的解释是:横向沿着能量流由耦合器和变速箱到电机和逆变器,纵向则是在自动化层次上对工业制造工艺控制结构和产品生命周期的集成。横向集成会改善机器的生产效率和产品质量,集成的产品包括变速箱、耦合器、电机和逆变器等,西门子作为老牌的驱动系统提供商可以提供“一站式”服务。
德国纽伦堡是西门子大型传动部生产工厂的所在地,汉诺威到纽伦堡的高铁列车的传动系统就是该工厂提供的。郭德辉是西门子大型传动部中国、中东和非洲业务发展总监,他举例说,亚洲最大的纸浆和纸张制造商之一亚洲纸浆纸业集团,通过使用全集成系统,能源消耗和造纸厂的二氧化碳排放量都大幅度减少。由此,亚洲浆纸业集团每条生产线年均节省数千万元的开支,年均停机时间被保持在最低的12.5小时。
工业4.0的其中一个核心元素是融合虚拟与现实世界,而全集成系统让CAD/CAM(计算机辅助设计、制造)工具和产品数据实现无缝交互。德国的机械制造商DMG正是通过这个方案,让虚拟模型生成现实机械的时间节省了80%。DMG还在网络化的生产中,通过优化虚拟生产计划和产品开发参数,使生产效率提高了50%。
未来工业企业需要对市场变化做出快速反应,即生产系统能对全球需求和特定客户要求做出快速反应。汉诺成博览公司董事约亨柯克勒说,在这一系统中,包括工件、机器到运输系统在内的所有环节都可以通过网络进行互联,实现彼此之问的自由通信,这就是所谓的智能工厂,但达到智能工厂之前必须进行“产业集成”。
很遗憾的是,要实现这一愿景,主要挑战之一则是标准化,即相关软件需要兼容所有联网的元器件、机器、设备和工厂等,当前每家公司的lT系统都使用独立的设置,要实现集成化发展,需要所有公司都采用业内广泛认可的国际化的标准生产体系。
西门子拥有驱动和自动化产品以及相关的软件支持,但它并不能要求客户都采用西门子的产品,尽管西门子有开放架构和思维模式。可见,未来智能工厂需要统一的标准体系。
数字工厂
西门子安贝格电子工厂坐落在德国巴伐利亚洲东部的安贝格市,它是全欧洲甚至全球最先进的数字化工厂。已经有24年历电的安贝格工厂为西门子提供印刷电路板等电子产品,100万次加工过程的差错率只有12次。
李永利是该电子工厂的副总经理,已经在此工作了3年以上,今年秋季他将被调回中国成都,担任西门子成都电子工厂的总经理。4月9日,记者在参访时,李永利解释了该工厂出错率从百万分之五百为何降到百万分之十二的背后故事。
制造业有一个公认的概念,作为全球最好的制造工人——德国工人的出错率大概在百万分之三百到五百,如果把这一比率降低到百分之十二,必须要靠机器来完成。安贝格工厂75%的生产过程是由机器来完成的,包括物料配送、数据收集、数据整理等,而其中最为关键的是智能算法的确定。
以前人们进行加减乘除要靠人工来计算,当计算器出现之后,没有人再怀疑计算器在加减乘除中是否算得准确,因为人们在制造计算器时已经把“智能算法”内置其中。工厂也是一样,以前需要用人工完成的动作通过“智能算法”固化在机器中,让机器代替人工来完成。在满是机器的工厂中,人的因素就是发号指令,做出生产管理决策,让机器去执行。
安贝格工厂有1万平方米的生产车间,生产线主要分为做印刷电路板生产和印刷电路板组装。当记者走进车间,眼前横排的一条生产线据说是1 5年前建立的,在这里看不到像其他很多工厂里工人们非常繁忙的样子,工人们很安静地在装有电脑屏幕的工位上有条不紊地工作着,并不是很忙碌。
当我们走进安贝格工厂时,李永利给记者呈现了两个世界,一个是真实的工厂,一个是虚拟的工厂。他说,在真实工厂之前就已经有了虚拟工厂,研发设计部门把虚拟的研发产品同步给生产部门来生产,两部门有着统一平台,并时刻保持着协调的一致性。真实工厂生产时的数据参数、生产环境等都会通过虚拟工厂来反映出来,而人则通过虚拟工厂对现实中的真实工厂进行把控。
为了更准确收集到生产过程中各种数据,安贝格工厂超过3亿个元器件都有自己的身份识别。“我们每个成品都有精确的生产信息,可以精确到单个产品中的每一个元器件,而每个元器件的基础信息都会有。这些基础信息包括哪条生产线生产的、用什么材质、当时用的扭矩是多少、用什么样的螺丝钉,等等。当一个元件进入烘箱时,机器会判断该用什么温度以及持续的时间长短,并可以判断下一个进入烘箱的元件是哪一种,适时调节生产参数。”李永利说
安贝格工厂的每一条生产线每天并不是一成不变地只生产一种产品,生产系统会实时同步研发部门的最新指示,自动跳转不同产品或者器件的生产模式。这种生产模式是研发和生产部门同步设定的,即研发部门的任阿变化都会实时在生产环节反映出来,生产系统会自动定格到每一个具体元件上并扫描它的参数。
安贝格工厂所有的设备都装有扫描器和读码器,产品和元件的所有信息都可以被记录下来。李永利作为生产环节的负责人对生产过程并不很关心,他每天关注的则是产品质量,一旦发现有问题,比如是原材料导致的质量问题,他会通过研发系统输入某个原材料有问题的指令,这一指令会下达到工厂控制层,所有生产线都能自动识别到,当扫描器和读码器扫描产品时,就会中止所有涉及该原材料的产品的生产。
记者在安贝格工厂看到,每个工人面前都有一台电脑屏幕,屏幕上都会显示即将需要执行动作图示,图示提醒他这步该做什么,所以工人不需要提前准备很多东西,也不需要之前做很多工作,只要对着电脑屏幕做就可以了。
在产品包装环节,旁边的电脑会详细记录人工或者机器是否往包装箱里投放了说明书、插件等,如果没有投放,电脑就不会打出产品的最终标签,这样就避免了漏放产品说明书的情况。要打的标签很重要,里面记录着有关产品的详细信息,这也是产品追溯时的关键依据。
安贝格工厂配有全自动化的立体仓库,会把原材料通过自动化的管线送到车问现场。记者在车问看到的都是整齐的生产线。但据李永利介绍,在车问下面还有像停车库一样的底层,原材料就是通过自动化的管线从立体仓库中被运送到车问现场,当然每一个原材料都有自己的身份标示。在车间现场有个临时站,原材料先从立体仓库被运送到临时站,等待随时被调用。
安贝格工厂的生产系统还与公司的ERP系统无缝对接,当某一订单生产完最后一个产品时,该订单将会在ERP(企业信息管理系统)中改变订单状况——生产完毕,成品就直接发货运走,工厂厂的生产完全是跟着订单走,都靠智能化的系统来完成。”李永利告诉记者说。
未来制造
西门子安贝格工厂尽管在世界上都属于最先进的工厂,但距离工业4.0所描绘的场景还有很大差距。西门子一直都是工业4.0的倡导者,鲁思沃认为: “这场变革将是一个渐进的过程,工业4.0的真正到来可能需要20年左右的时问,在此期问,变化将不断出现和递进。”
鲁思沃把这个“渐进的过程”称作为工业3.X,它是建立在强大的生产执行系统和数字化企业平台基础上,虚拟世界和现实世界中的生产通过数字化互联融合,可以令整个生产价值链的数据进行无缝交流。
德特勒夫.凯瑟博士是麦肯锡咨询公司德国汉堡分公司总监,是制造业管理规范方面的专家,他强烈地感觉到全球化趋势正在剧烈改变着制造业的场景,将对现有制造业产生巨大冲击。当然他电认为,新的机会则会在更加复杂和不确定性的环境中诞生。
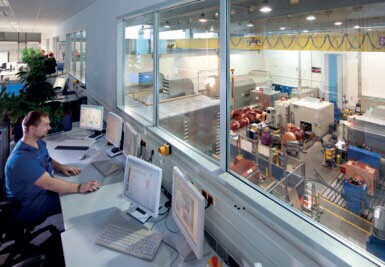
凯瑟博士强调了不确定性将成为制造业的常态,这些不确定性包括原材料和能源价格的变化、汇率的波动、供应链的复杂性、新兴市场的高成长性、贸易规则的变动、自然灾害以及人才和知识产权的约束等,这些因素都有可能引发全球制造业供应链的巨大灾难。
IT、循环经济、虚拟设计、3 D打印机器人、纳米和复合材料等关键技术正在对传统制造业产生严重影响,很多德国公司已经开始把新材料、人机交互和工业4.0作为引发公司未来商业变革的最重要的因素,其中作为工业4.O序曲的数字工厂正在改变德国现有工厂结构和价值链。
是否重视制造业向工业4.O的过渡,默克尔甚至认为“这是德国工业是否拥有未来的关键”。根据德国高科技企业联合会发布的研究报告,未来l 0年工业4.0进程将为德国带来2670亿欧元的产值,并认为工业4.0将在机器设备、汽车、电子、信息工程、化学等领域获得率先突破。
鲁思沃把工业4.0时代细化到三个关键维度:第一是生产执行系统、数字化企业平台、产品生命周期管理软件和自动化系统的集成,将带来一个强大的制造运行管理系统j第二是虚拟世界和现实世界生产的融合,基于统一的数据模型来完成,制造商可因此大大缩短产品的上市时间;第三是信息物理融合系统,这也是增加生产灵活性、缩短产品上市时间的关键,互联的机器可以通过网络技术彼此交流,并灵活地集成于现有的生产过程中。
与鲁思沃相比,德特勒夫.凯瑟博士对工业4.O的理解相对比较简单,他认为就是互联网在传统制造业中的应用,只是互联网应用之前必须进行数字化。但凯瑟博士所理解的数字化工厂较为复杂,其中包括无处不在的智能传感器、无处不在的无线互联网以及对数据处理更加灵活和智能化的系统。
他举例说,未来制造中的生产线将由原来僵硬的、静态的、为特定产品设置的流水线生产,向更加灵活、动态的、为个性化订单设置的柔性生产过渡。
“数字化生产为制造商提供了至关重要的灵活性,并带来更高的生产效率”,这是英国《经济学人》以案头调研和专家深度访谈后得出的结论。报告认为,网络化生产系统利用数据流对生产进行控制和优化,使小批量制造和定制生产成为可能。由此,它可让制造公司更具灵活性,从而更好地对市场需求做出响应。
当然,生产制造的网络化和数字化程度不断提高,也带来了人们对新的网络安全的担心,黑客攻击、病毒侵入、网络瘫痪等这些可能随时发生的事件将对智能工厂产生致命冲击。所以,网络安全将是未来制造值得警惕的问题。
西门子是全球最具创新能力的企业之一。广州丙通MRO将致力于在和西门子公司涉足的所有业务领域引领技术发展潮流,专注于通过我们的技术为客户及其它利益相关群体带来切实的利益。我们将把更多的精力投入到为满足当地客户需求的产品及解决方案。同时,利用西门子的资源优势推动中国技术发展,并向全球技术创新作出贡献。
本文地址:http://www.btone-mro.com/BtoneInform/newsContent.aspx?id=3634